Brush plating
One special procedure used frequently for repairs and finishes in galvanic technology is brush plating.
Among the preferred applications of this process are dimensional corrections and the repair of blank areas on machine components or the retroactive plating of work pieces that have already been galvanized.
Functional process:
To apply a galvanized layer to metal surfaces, two different methods can be used: galvanic immersion and pen or brush plating.
During the immersion galvanic process, the work piece to be coated and the anode are immersed into an electrolyte, through which electrical power is directed for some time. This process allows for the application of even extremely thick metal coatings to the work piece.
The disadvantage is that a large volume of electrolytes is needed to fill up the immersion pool. Moreover, immersion galvanic processes can only be used in stationary situations.
For brush plating, the component to be plated is attached to the minus pole of the galvanic system. Individual anodes that have been precision manufactured are encased by a cotton tampon. Next, the anode is evenly guided across the surface to be coated.
The metal ions that travel from the electrolyte to the cathode generate the desired metal layer.
Given the small and special components, brush plating can be used in a geographically flexible manner and offers a vast spectrum of possible coatings for corrosion protection, which can be adjusted to the needs in terms of hardness and functions.
Thanks to the high flexibility and dependability of this process, it is an optimum approach to the repair of complex components and/or machines.
Overview of the benefits of brush plating:
- Repairs or plating work of partial surfaces can also be performed on site
- In most cases, the dismantling of complex components is not necessary-> it is possible to work on very large components as well as those that are still installed
- The production of custom anode forms makes it possible to specifically and partially plate large and complex forms and work pieces without having to perform time consuming uncovering work
- The work piece is not heated up
- Hence, the structure is not altered and there is no tension build-up in the work piece
- The process can be used with all electrically conductive materials
- High surface hardness
- Improved fatigue strength as well as wear and tear resistance
- Good corrosion resistance
- The work piece is instantly usable after processing
- High cost savings yield compared to new acquisition cost
Overall, Rudolf Clauss offers flexible and agile options with its specialized brush plating processes, such as:
- Nickel layer thicknesses of 100,300 µ or more that are a placed in a targeted manner, make it possible to restore damaged or worn component elements.
- Hardness levels of up to 600 HV
Thanks to specifically adapted nickel electrolytes, it is possible to attain the strongest hardness levels - Repair of hydraulic cylinders that are damaged in spots, restoration of shafts or axles
- Coating in partially hard to reach areas of any geometry or selective new plating possible in the event of adhesion problems
The spectrum of possible coating metals is vast and usable for every requirement.
With this technology, it is possible to repair and protect against wear and tear as well as corrosion for instance the surfaces of turbines, shafts, coupling seats, cast iron panels, print rollers, hydraulic cylinders, piston rods, extruder screws, cast iron forms, etc.
Given the fact that we can repair damages by mobile means and at the customer’s location, we minimize the costs you would incur as a result of new acquisitions, expansions, transportation or the application of completely new plating.
Rudolf Clauss is DALIC’s exclusive partner for Germany
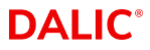
DALIC is one of the originators of this technology.
Thanks to this strategic partnership, Rudolf Clauss GmbH & Co. KG has at its disposal exclusively certified processes in cooperation with DALIC. This translates into the high level of flexibility and reliability of these processes, especially in the field of repairs of complex components and machines.